In a world where manufacturing can sometimes feel like watching paint dry, virtual reality swoops in like a superhero, ready to save the day. Imagine donning a VR headset and stepping into a vibrant, interactive factory floor where machines dance to your command and processes unfold in 3D. It’s not just sci-fi; it’s the future of manufacturing, and it’s here to transform how things are made.
From designing prototypes without the mess to training employees in a risk-free environment, virtual reality offers manufacturers a playground of possibilities. This tech isn’t just cool; it’s a game-changer that boosts efficiency and slashes costs. So, buckle up as we explore how VR is revolutionizing the manufacturing landscape, one headset at a time. Who knew the factory of the future could be so much fun?
Virtual Reality in Manufacturing
Virtual reality (VR) revolutionizes the manufacturing sector by providing immersive experiences that enhance design, training, and operations. Users interact with detailed 3D models of products and assembly lines, enabling real-time adjustments and assessments. These dynamic simulations facilitate rapid prototyping, allowing designers to visualize concepts without physical prototypes.
Training processes benefit significantly from VR environments. Employees engage in safe, controlled scenarios that replicate real-world conditions. These immersive training sessions enhance skill acquisition without the risks associated with traditional methods. Trainees can practice various procedures repetitively, reinforcing knowledge while reducing error rates.
Collaboration in manufacturing transforms with VR technology. Teams can share virtual spaces, regardless of geographical locations, enabling simultaneous participation in design discussions and problem-solving sessions. Enhanced communication and visualizations improve decision-making speed and accuracy.
VR’s impact extends to maintenance and troubleshooting. Technicians equipped with VR headsets access detailed guides and instructions tailored to specific equipment. This hands-on support minimizes downtime, ensuring quicker repairs and sustained productivity levels.
The integration of VR in manufacturing contributes to significant cost reductions. Companies experience savings from decreased material waste and enhanced training efficiencies. As VR adoption grows, manufacturers position themselves to adopt innovative practices, leading to better product quality and faster time-to-market.
Data from recent studies shows that organizations leveraging VR report up to a 25% increase in efficiency across various operations. Those investing in VR training programs see higher retention rates and improved employee satisfaction. The overall potential of VR in manufacturing continues to unfold, demonstrating its vital role in shaping the industry’s future.
Benefits of Virtual Reality in Manufacturing
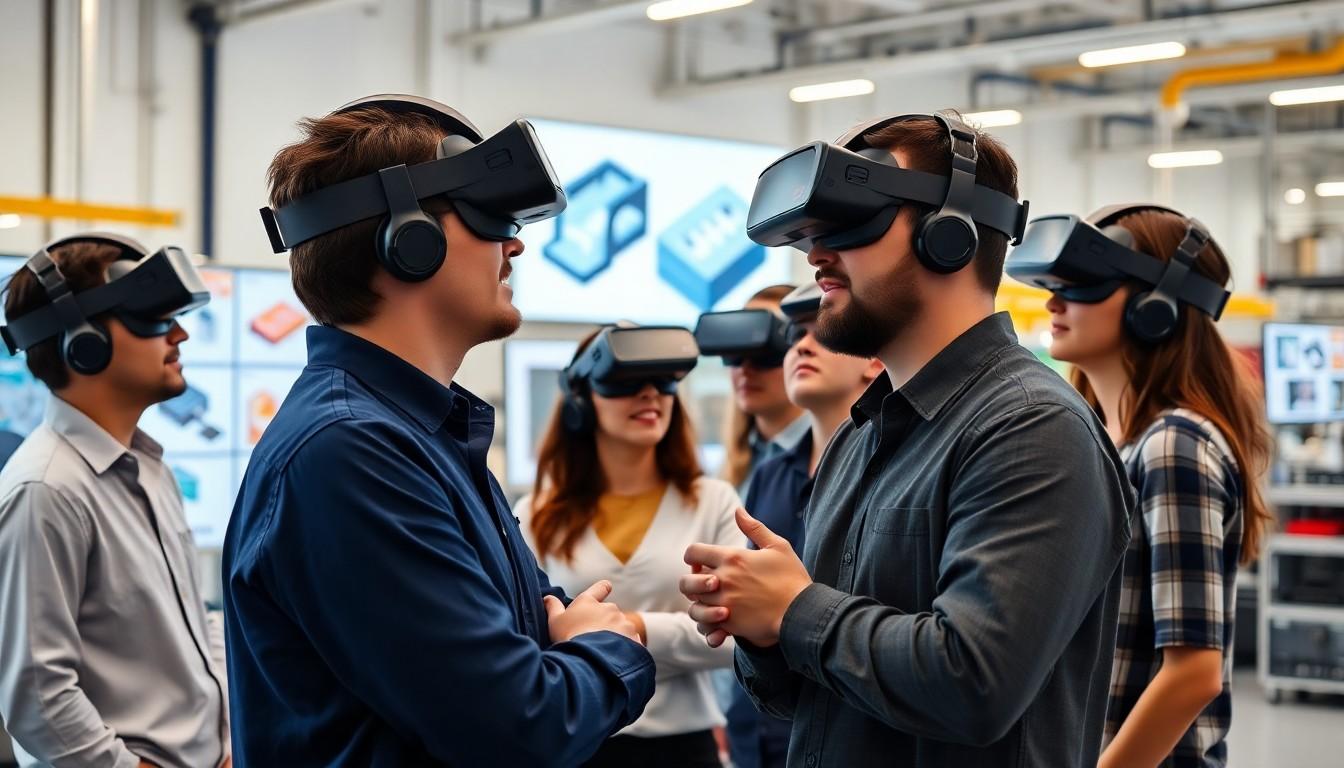
Virtual reality significantly enhances various aspects of the manufacturing sector, allowing companies to leverage interactive technology for better outcomes.
Enhanced Training and Skills Development
VR provides a safe learning environment that closely mirrors real-world manufacturing scenarios. Employees engage with realistic simulations, leading to deeper understanding and retention of processes. Repetitive practice within VR setups reduces the likelihood of errors during actual operations. Organizations witness improved employee confidence and competence as individuals refine their skills in a controlled space. Additionally, studies show that companies using VR for training report a 30% reduction in training time, improving overall productivity.
Improved Workflow and Design Processes
Streamlined design processes occur when teams utilize VR to interact with detailed 3D models. Collaboration improves as multiple members can access the same virtual environment regardless of physical location. Real-time adjustments to prototypes enhance innovation and creativity. Furthermore, VR enables faster identification of design flaws before physical production, significantly cutting down on material waste. Companies adopting VR witness up to a 25% increase in efficiency and a notable decrease in time to market, aligning with the industry focus on lean manufacturing practices.
Challenges in Implementing Virtual Reality
Implementing virtual reality in manufacturing presents several challenges that organizations must navigate effectively.
Cost and Resource Allocation
Investing in VR technology demands substantial financial resources. Companies face initial costs for hardware, software, and training personnel on new systems. Long-term maintenance and updates further strain budgets. Effective cost allocation becomes essential; organizations often struggle to balance short-term expenses with potential long-term benefits. Additionally, unexpected costs can arise during implementation phases, complicating budget forecasts. Engaging stakeholders with a clear breakdown of potential returns on investment enhances budgetary discussions, making it easier to secure necessary funding for successful VR deployment.
Technological Limitations and Integration
Technological limitations pose significant hurdles for manufacturers adopting VR. Compatibility issues between existing systems and new VR technology often arise, leading to integration challenges. Legacy systems can hinder seamless data transfer, resulting in inefficiencies. Moreover, not all VR solutions provide the required fidelity needed for specific applications. Inadequate training can exacerbate these issues, as employees may struggle to adapt to new workflows. Ensuring comprehensive training programs alongside robust technology assessments allows organizations to mitigate risks linked to integration obstacles. Investing in user-friendly platforms also contributes to smoother transitions and better overall experiences.
Case Studies of Virtual Reality in Action
Virtual reality (VR) has significantly impacted manufacturing through various case studies demonstrating its capabilities. Organizations leverage VR to drive efficiency, enhance training, and streamline operations.
Successful Implementations
Siemens employs VR for product design and prototyping. Engineers use immersive simulations to evaluate designs before physical production, reducing material waste. Another example is Ford, which integrated VR into its design process. Teams collaborate in a shared virtual environment, improving communication and accelerating decision-making. Boeing utilizes VR for assembly line training. New technicians practice procedures in realistic scenarios, resulting in a 30% decrease in training time. Companies also report enhanced safety and reduced error rates, leading to better overall product quality.
Lessons Learned from Failures
Some implementations of VR face challenges. General Electric experienced setbacks when attempting to integrate VR for maintenance training. The firm struggled with hardware compatibility, leading to delays and increased costs. A different case involved a car manufacturer where employees found VR interfaces difficult to navigate. Feedback from users highlighted usability issues that hindered engagement. Additionally, inadequate initial training for technicians caused confusion, resulting in lower productivity. These examples show that companies must ensure comprehensive training and address compatibility concerns before fully integrating VR solutions.
Future Trends in Virtual Reality for Manufacturing
Advancements in virtual reality (VR) technology continue shaping the manufacturing sector. Emerging trends emphasize enhanced training and simulation techniques, further improving employee preparedness and safety. Companies increasingly adopt VR for design validation through virtual prototypes, minimizing material waste and streamlining production processes.
Integration of augmented reality (AR) with VR is gaining traction, allowing real-time data overlays during manufacturing operations. Enhanced maintenance solutions use VR to provide technicians with step-by-step instructions, significantly reducing downtime. A notable shift toward cloud-based VR solutions enables remote collaboration, allowing teams to interact in virtual environments from various locations.
Employers report substantial gains in employee retention and satisfaction due to VR training programs. In fact, organizations utilizing VR experience up to 25% efficiency gains, indicating a strong correlation between VR use and operational success. These immersive experiences amplify creative problem-solving by allowing employees to explore scenarios in safe, simulated settings.
Studying user interface improvements is essential, as companies seek to overcome usability challenges experienced in earlier VR implementations. Success hinges on selecting intuitive platforms that simplify the onboarding process for employees. Future VR systems will likely focus on optimizing compatibility with existing technologies to foster seamless integrations.
Investment in sturdy VR infrastructure will remain critical for manufacturers aiming to harness these benefits. Companies that allocate resources wisely toward VR training and system functionalities witness significant competitive advantages. As VR technology evolves, its application in manufacturing will become increasingly sophisticated, leading to more effective and innovative processes.
Reshaping The Industry Landscape
The integration of virtual reality in manufacturing is reshaping the industry landscape. Companies that embrace this technology are not only enhancing training and collaboration but also achieving significant efficiency gains. As VR continues to evolve, its applications will become more sophisticated, driving innovation and streamlining processes.
While challenges exist in implementation, the potential benefits far outweigh the hurdles. Organizations that invest strategically in VR infrastructure and training will position themselves for long-term success. The future of manufacturing is not just about adapting to change; it’s about leveraging cutting-edge technology to stay ahead in a competitive market.